
@MonsterFairings
Motorcycle Fairings
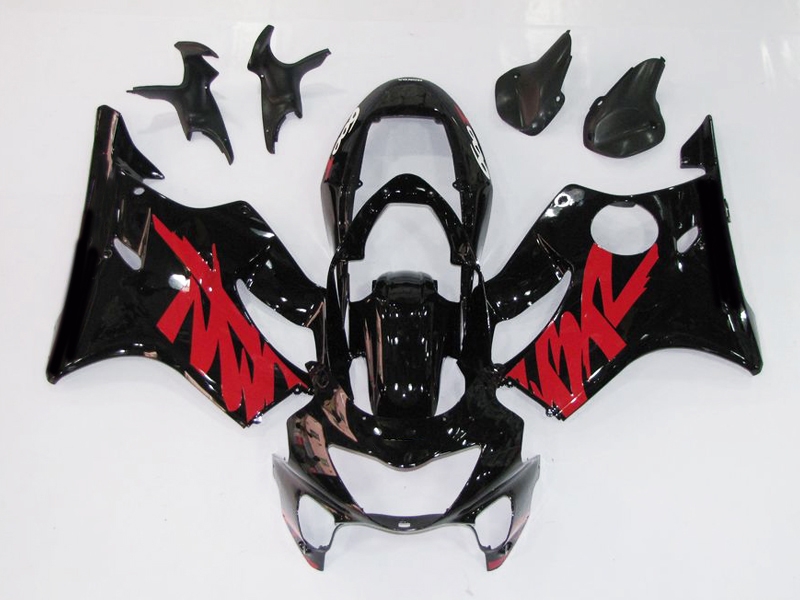
Motorcycle fairings can be made from several different materials ranging from metals, plastics and fibreglass to newer composites such as carbon fibre. The importance of streamlining was known very early in the 20th century. Some streamlining was seen on racing motorcycles as early as the 1920s.
The term fairing came into use in aircraft aerodynamics with regard to smoothing airflow over a components where airflow was disrupted. Early streamlining was often unsuccessful resulting in instability. Handlebar fairings, such as those on Harley-Davidson Tourers, sometimes upset the balance of a motorcycle, causing instability. The introduction on the BMW R100RS in 1976 marked the beginning of widespread adoption of fairings on sports and touring types of motorcycles. Originally, motorcycle fairings were cowlings put around the front of the vehicle, increasing its frontal area. Gradually, over time they became an integral part of motorcycle design. Modern motorcycle fairings increase the frontal area at most by 5% compared to a naked machine. Fairings mostly carry headlights, instruments, and other items. If the fairing is mounted on the frame, mounting equipment on the fairing reduces the weight and inertia of the steering assembly, improving the handling.
Over the years motorcycle fairings have changed in their composition over the years. Most motorcycle fairings are made from acrylonitrile butadiene styrene (ABS). ABS is a plastic commonly used in sport bikes and certain aftermarket fairing manufacturers due to its strong, flexible and light weight properties. The advantage of ABS over other plastics is that it combines strength and rigidity, while also being tough.
There are two common methods of producing an ABS plastic fairing: injection and compression moulding. During injection moulding, ABS plastic is melted and injected into the mould cavity. Constant pressure is applied to allow for material shrinkage. The plastic then cools and hardens in the mould. Injection moulds allows for uniform thickness throughout the entire piece. It gives the most accurate end product that can be produced uniformly every time. This is how we make our fairings at Monster Fairings, as it is the most reliable way to make strong and high quality parts. ABS can also be compression moulded. During compression moulding, the plastic is generally preheated and placed into a heated metal mould cavity and pressure is applied to force the plastic to take the shape of the mould. Heat and pressure is applied until the plastic cures in the mould. The excess plastic is then cut away and removed from the mould. Disadvantages to compression mould include varying product consistency and flashing, which is excess material attached to the moulded part that needs to be removed where two or more parts of the mould meet.
Another option to make motorcycle fairings is using composite materials such as fibreglass and carbon fibre. Fibreglass is made of woven glass fibres, and is used as a reinforcing agent for many plastic products. The composite is known as glass-reinforced plastic (GRP), is normally referred to by the name of its reinforcing material. Fibreglass fairings are commonly used on the race track. In most cases fibreglass is lighter, and more durable than ABS Plastic. Damaged fibreglass can be repaired by applying new layers of woven fibreglass cloth mixed with a polymer such as epoxy over the damaged area, followed by sanding and finishing.
Carbon fibre reinforced plastic (CFRP) is the lightest, but most expensive, fairing material available today. The fairings are made by exactly the same process as with GRP. However, the woven fibres are carbon instead of glass. Carbon fibre has a higher strength to weight ratio than GRP and is mostly used on the race track. Due to this, there is also a reduction in weight and size of fairings, as less material can be used to create fairings of the same strength as other fairings.